Investigative Design of a Prosthetic for an Individual with a Congenital Limb Deficiency
Undergraduate Research Opportunities Program - UCI (June 2018 - June 2019)
Background
After watching Hugh Herr's Ted Talk concerning the design of mechatronic prosthetic legs, I was interested in learning more about prosthetic design. From my 3D printing experience, I thought it would be a great opportunity to go through the design process from characterizing the anatomical performance of a user pre-prosthetic, to designing and implementing a prosthetic.
After contacting Professor David Reinkensmeyer, who led UCI's Bio Robotics lab, we found that the best medium to pursue this endeavor was through UCI's Undergraduate Research Opportunities Program (UROP). Additionally, another member of the lab was able to connect me with a peer with a congenital limb deficiency of the left hand (for privacy, the participant will be anonymous). The participant was interested in helping contribute to the project, and would be the main user of the prototyped prosthetic. As the project grew, I decided to encourage some of my peers to join the project, which later turned into a team of 4 engineering students in total.
Abstract
A congenital limb deficiency is a condition where an individual has a limb deformity developed from birth, which differs from acquired amputations which are typically attributed to injury or other complications which may require surgical amputation. We were interested in understanding the benefits of a purely mechanical prosthetic device for an individual with a congenital limb deficiency of the left hand. Through developing such a prosthetic device, we hope to understand the improved ability the prosthetic provides the user, and cater the design of the prosthetic device to user specific needs. At first, these needs were to rock climb and to perform dexterous tasks. Due to the structural limitations of 3D printed FDM material for prototyping and limited resources based on the scope of the project, the user needs were constrained to develop a prosthetic capable of performing dexterous tasks. By performing DOF tests, we were able to categorize the abilities of the biological limb. To verify the effectiveness of the prosthetic, SHAP tests were performed, comparing the deficient hand with the prosthetic device.
Performance Characterization
We wanted to baseline the performance of the congenital limb deficiency compared to the unaffected hand. hand movements were characterized based on the guidance from reference (1). Including but not limited to Forearm supination and pronation, wrist extension and flexion, and other movements. These are visualized below.
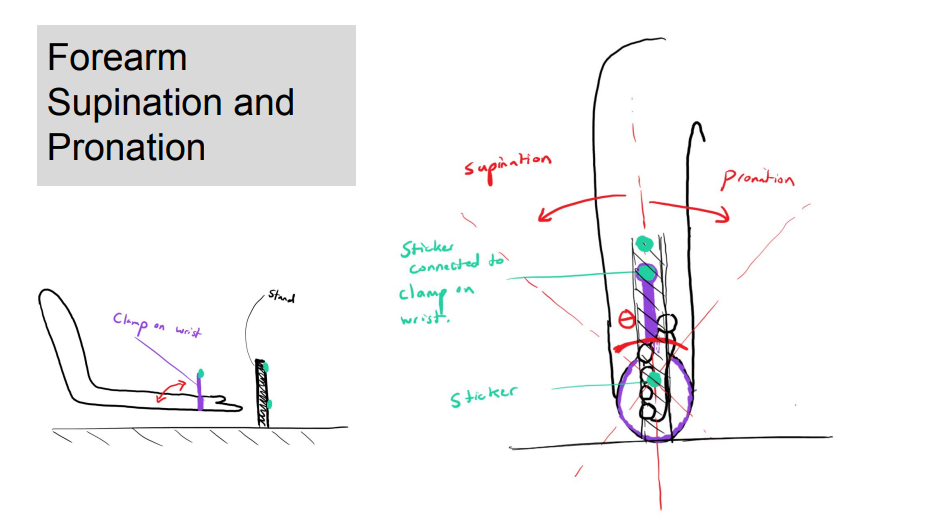
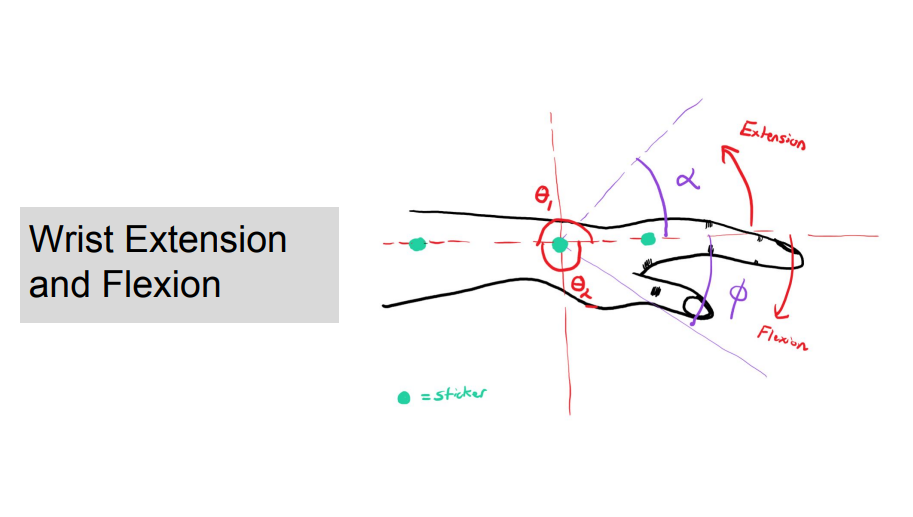
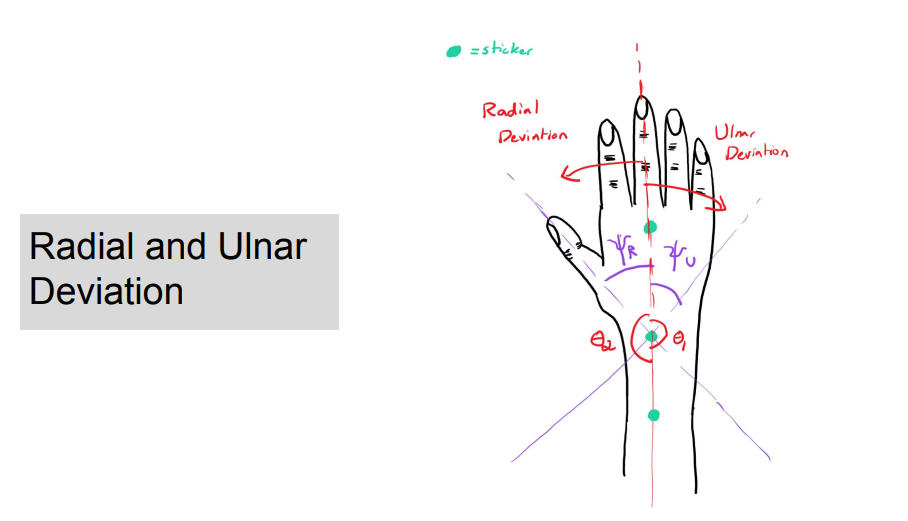
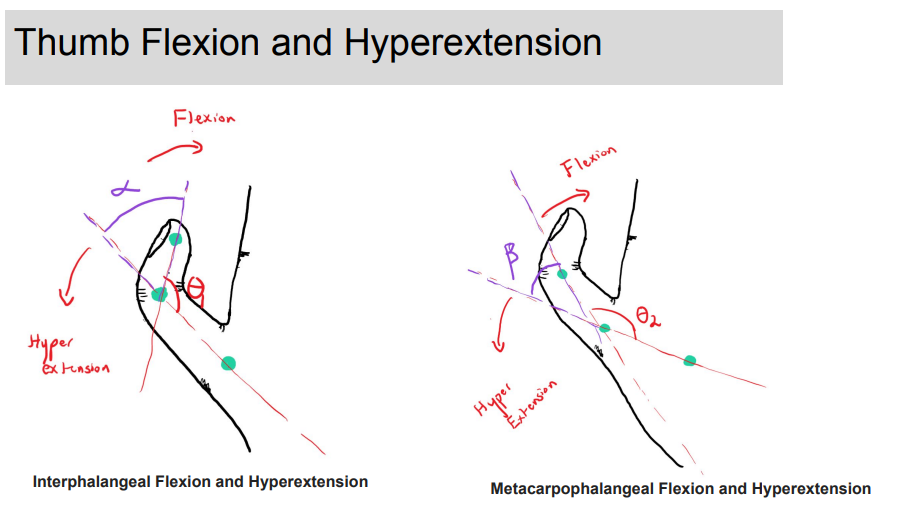
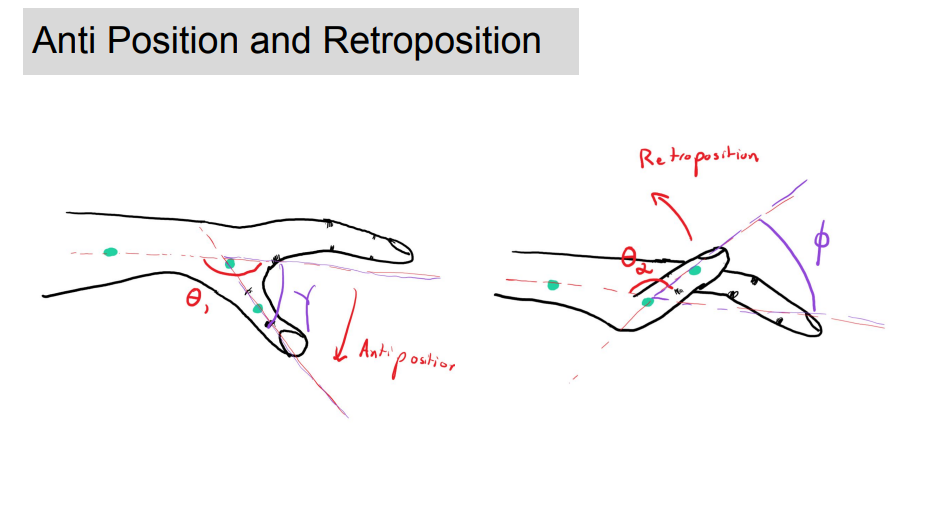
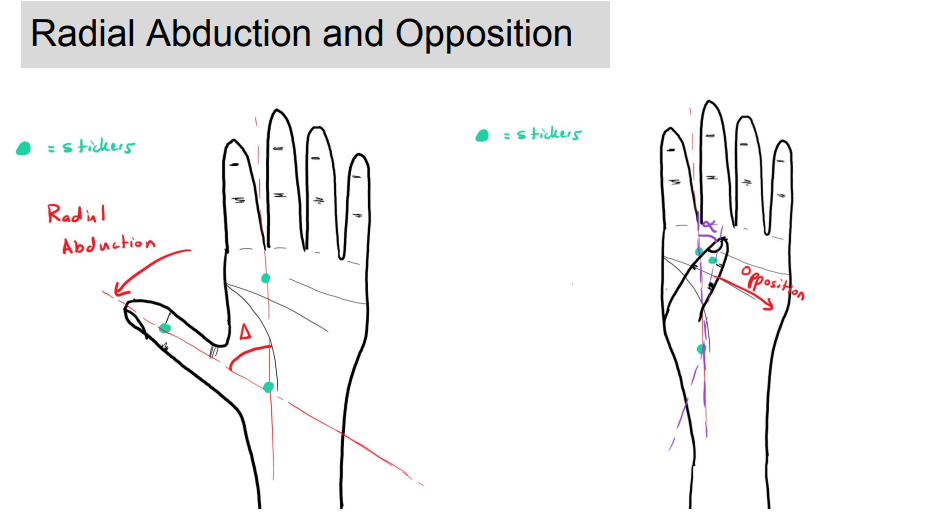
Once the target movements were defined, fixturing was developed to help in characterizing these motions. Along with this was the use of a visual software called Dartfish which would help track key points of movement completely through video and without the use of special hardware, such as encoder equipped fixtures. Examples of the video data are shown below for raw data and processed data.
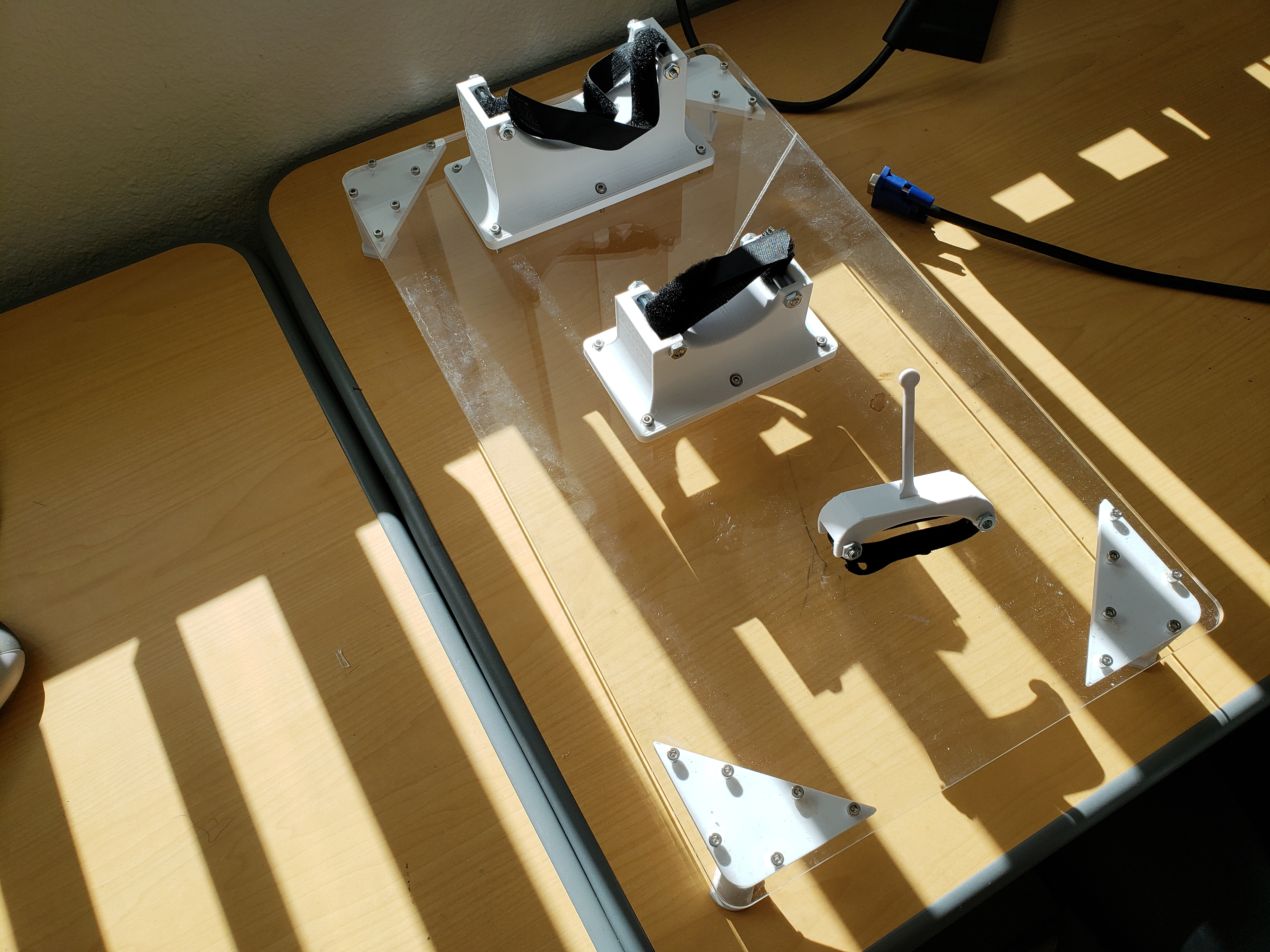
Radial Abduction and Opposition
Unaffected Hand, prior to addition of Dartfish video tracking.
Radial Abduction and Opposition (Left) & Metacarpo-Phalengial Flexion and Hyperextension (Right)
Congenital Limb Deficient Hand, post Dartfish video tracking.
Supination and Pronation (Left) & Wrist Flexion and Extension (Right)
Congenital Limb Deficient Hand
Baseline Comparison
Based on the testing outlined above, each maximum movement was characterized in degrees and plotted on a radar chart as shown below. Although this would not be used as a driving metric to verify the effectiveness of the prosthetic design, this was helpful in understanding how the congenital deficient hand compared to an unaffected hand.
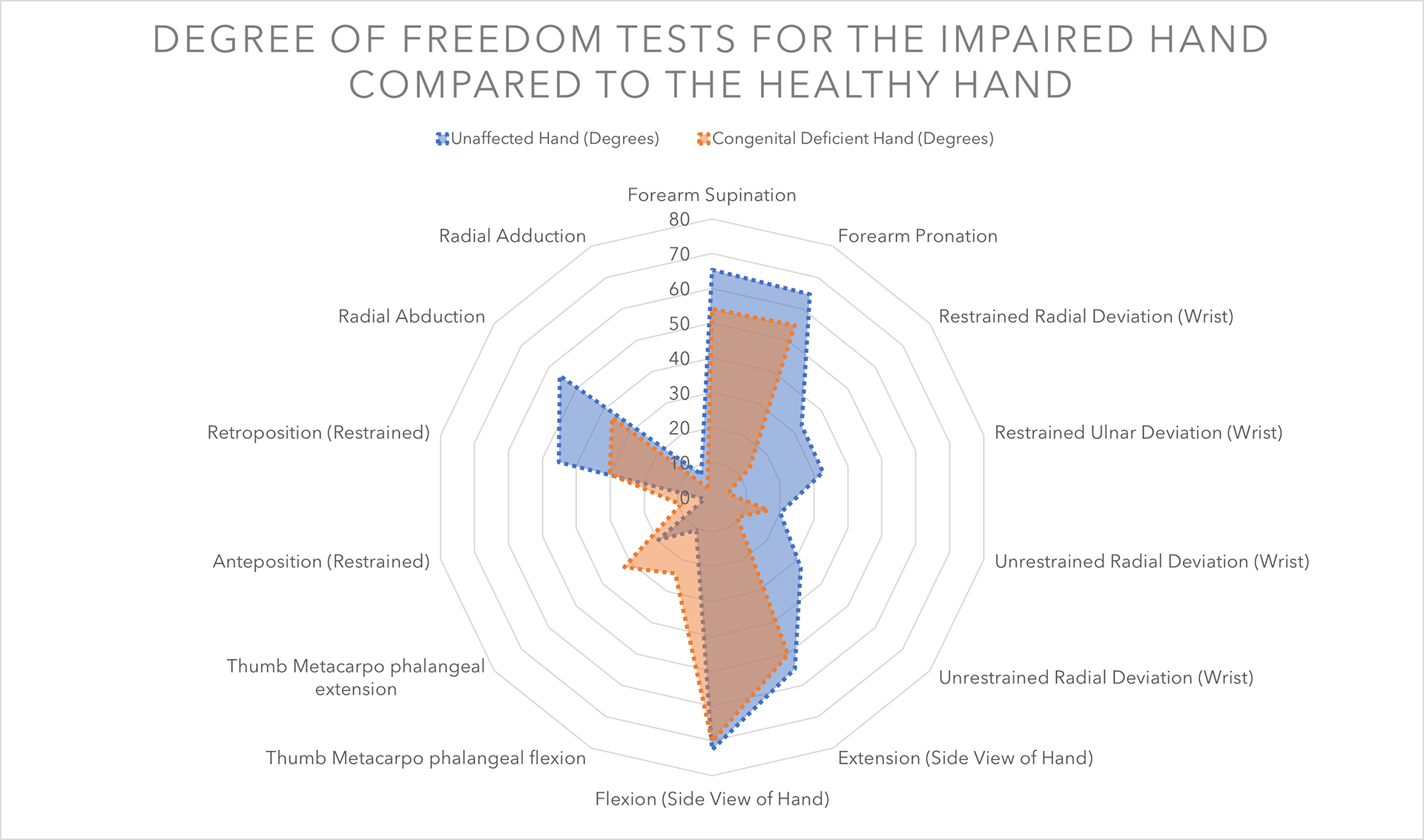
Modeling the Affected Hand
A mold was first created of the affected hand using a 300Q Smooth Cast Urethane Resin. The first attempt to convert the cast into a 3D virtual model was done using photogrammetry. various attempts of this method were performed, first with no background, followed by a black backdrop, and finally no background with black cross markers. In all attempts, collecting 40 - 50 photos, no successful model was achieved. See the right for the photogrammetry attempt, followed by the raw photos below.
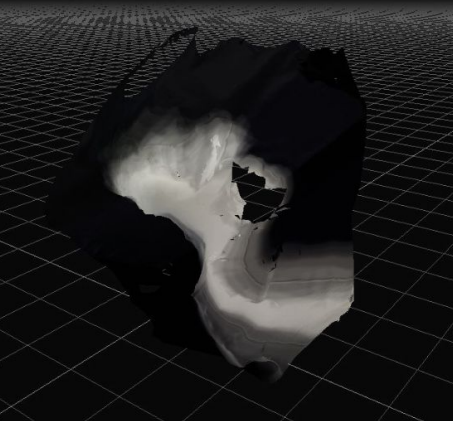
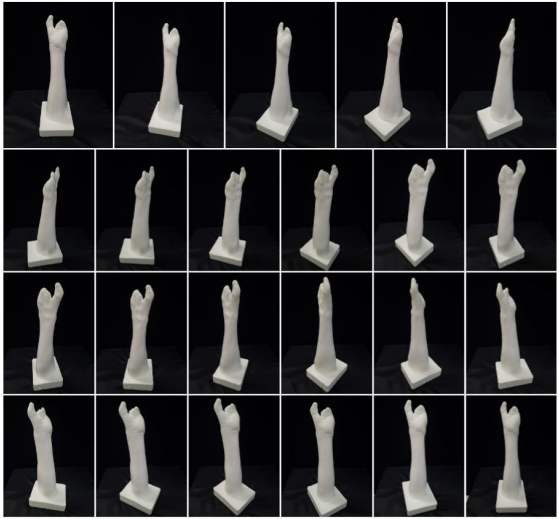
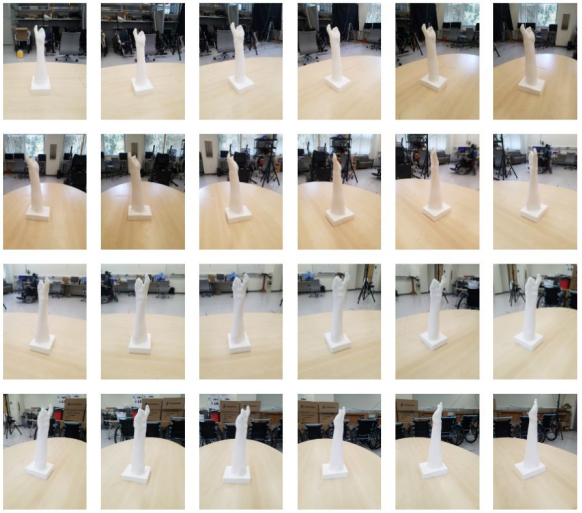
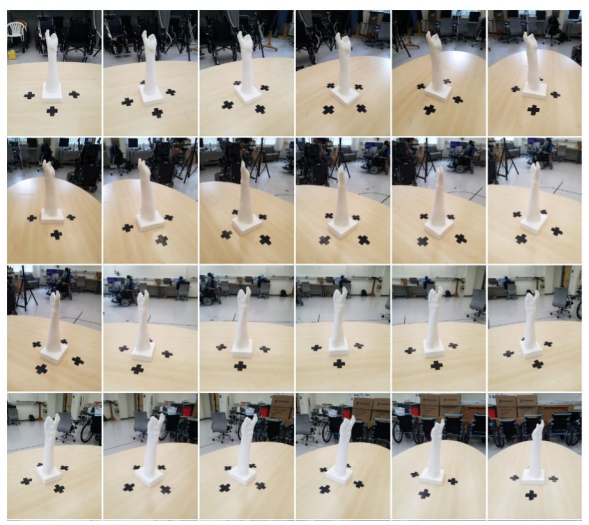
Given this unsuccessful attempt, a NextEngine Scanner was used to generate a laser scanned model of the affected limb. This would be converted to a Parasolid file and be used for further modeling of the prosthetic.
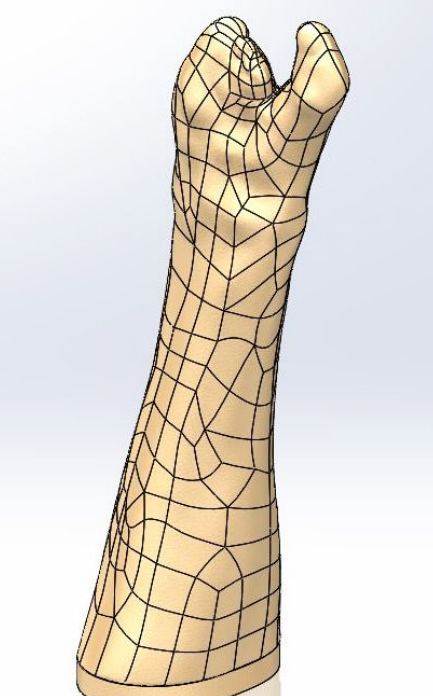
Creating the Basic Forearm Interface
The forearm profile was the initial focus of the early design stages of the prosthetic. This was done by taking various offset cross sections along the Parasolid scan. These offset cross section profiles would then be lofted to form the general forearm interface of the prosthetic.
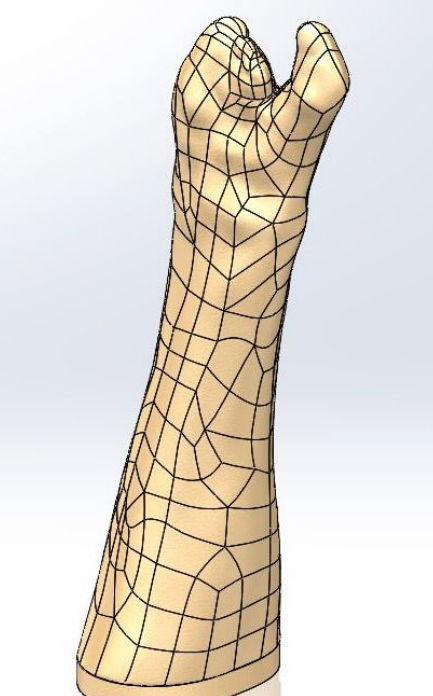
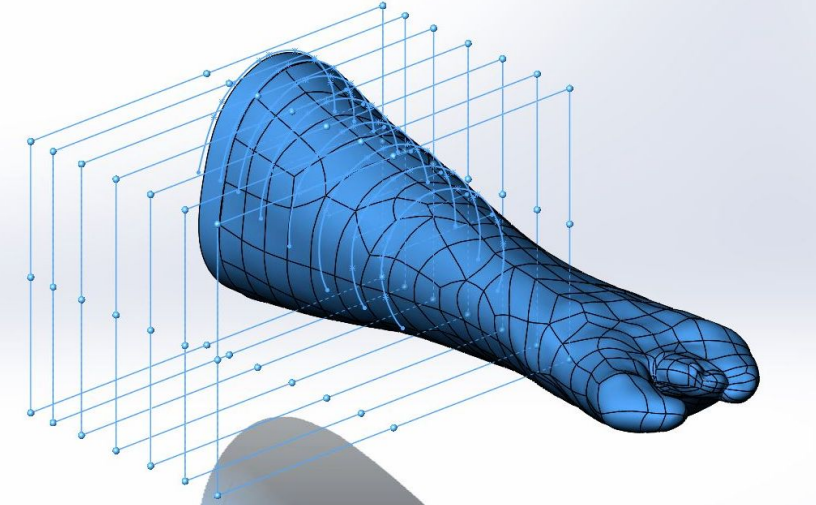
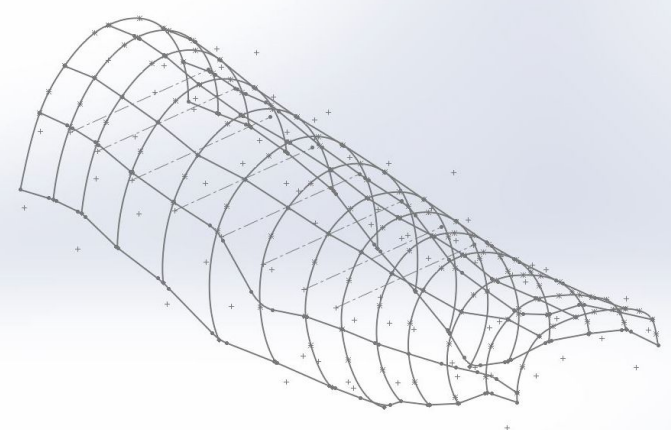
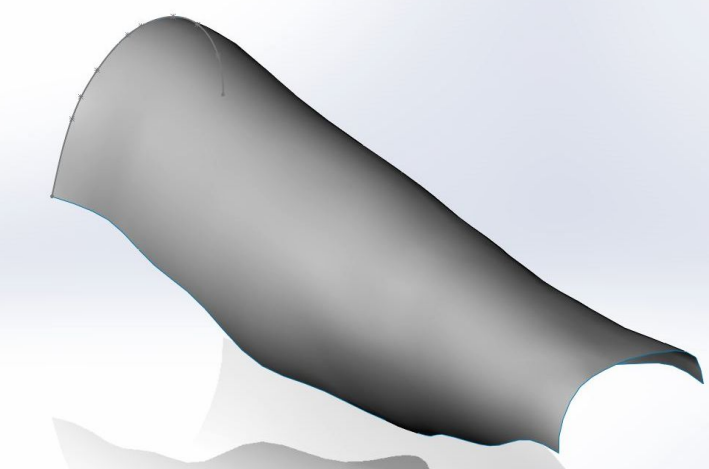
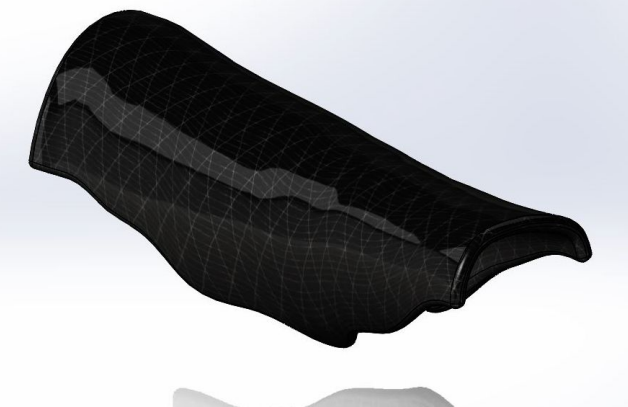
Forearm Mounting and Wrist Design
The forearm mounting was designed to conform to the forearm with an insert-twist method, where the user would slide in the forearm sideways to the interface, then twist the forearm 90 degrees to secure it in place. To better help with security, slots were made for velcro straps. Additionally, the approximate anatomical position of the wrist rotation point was determined through the DOF video testing, and was approximated to the SolidWorks model.
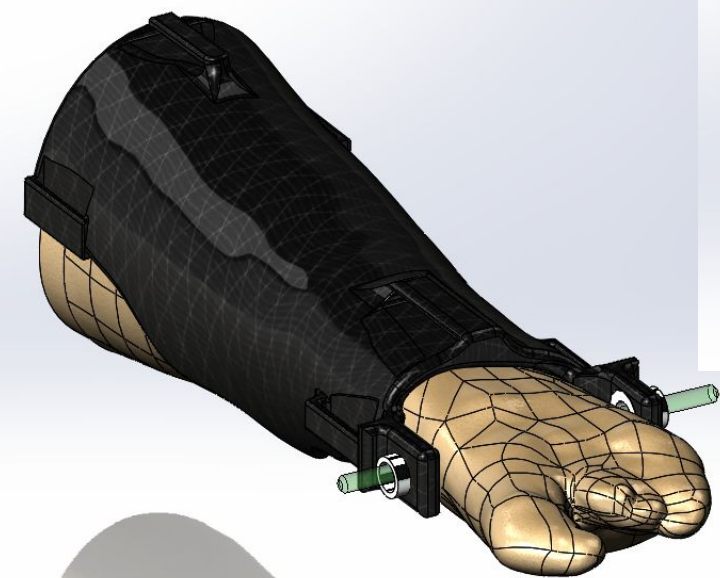
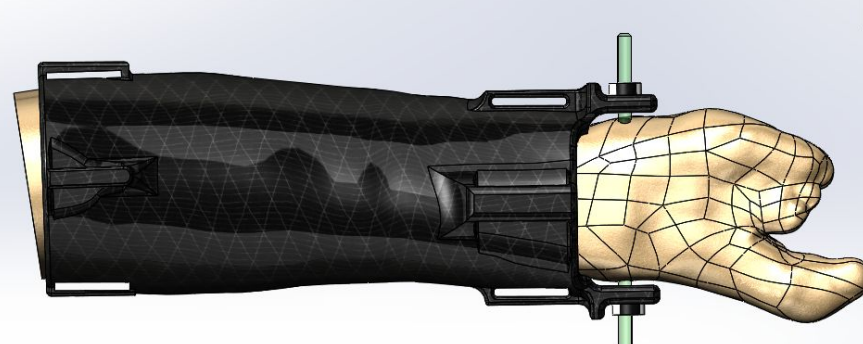
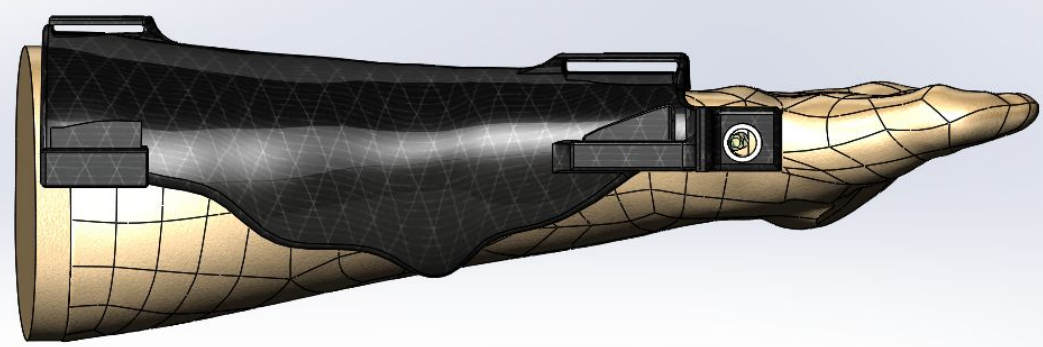
Passive Prosthetic Iteration
To get general feedback on the fit and basic function of the prosthetic, a passive design was prototyped. The design was adjusted to add ventilation and a usable passive hand for the user.
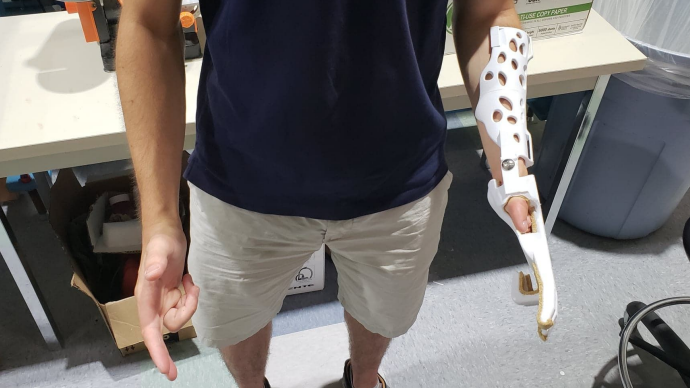
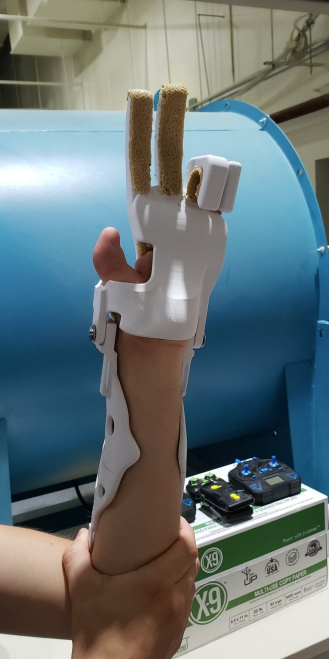
Finger Actuation - Iteration 1
Finger actuation was assessed through a literature review of existing actuation methods. Various methods were observed, such as single actuator linkage fingers, to a cable driven ratcheting technique. The challenge with the intended user's case is that many cases we found in the literature review were either complete hand amputations, or partial finger loss. In this way, it is much simpler to design a prosthetic around these anatomical parameters. In the case of a full amputation, the design intent is targeted to developing a complete prosthetic mirroring the lost anatomy. In a partial acquired amputation, the design can rely on parts of the hand that mimic typical anatomy. In a congenital case however, the hand anatomy does not mimic typical anatomy, both in form and function, and therefore poses a design challenge. See below some alternatives discovered in the literature review.
Cable Driven Design
(2)
Linkage Design
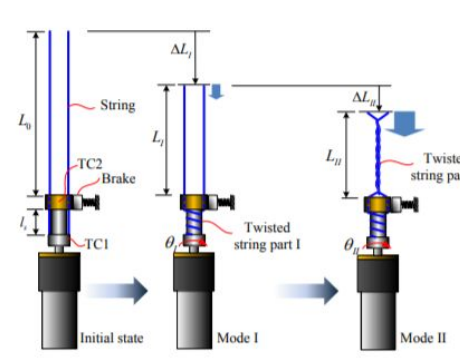
As a first attempt, a cable driven and ratcheting system was pursued for finger actuation. This design used ratcheting components from a wrench and 3 separate 3D printed joints to simulate the proximal, medial, and distal portions of the finger. Although the actuation appeared to somewhat mimic the performance of a finger, the main drawbacks were:
1) The system was not fully constrained, and so one cable length input could result in two positional outputs. That is, the mobility of the system was > 1.
2) The system did not have much structural integrity, particularly at the joints.
3) Cable routing would be a challenge, especially considering the cable would be load bearing.
With these drawbacks in mind, this design approach was tabled for possible further investigation, though was ultimately not revisited.
Finger Iteration 1 Design Layout
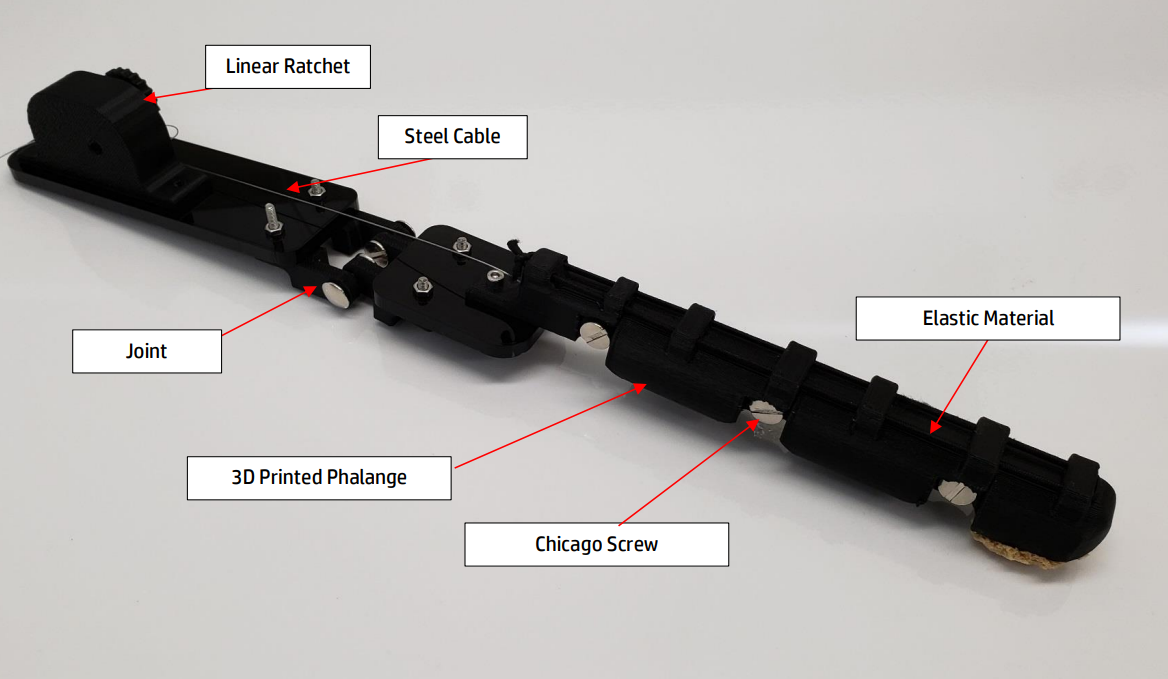
Finger Iteration 1 Mobility Issue
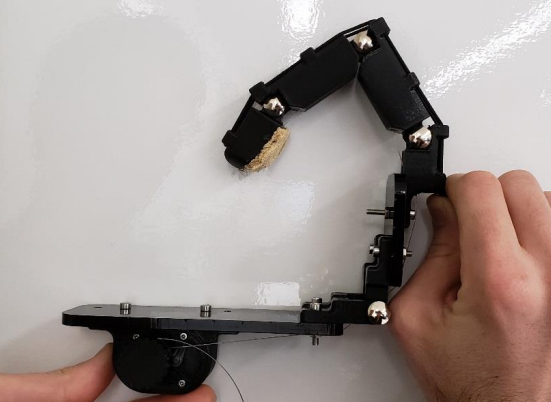
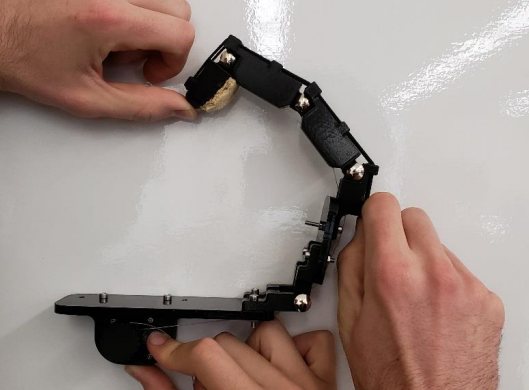
Finger Iteration 1 Functional Behavior
As the pivot joint mimicking the palm is rotated, the length in spanning the top finger phalanges is reduced. This pulls the finger inward and curls it as shown. When the cable tension is released, elastic line spanning across the top finger phalanges (which are in tension) pull the finger back to the neutral position.
Finger Actuation - Iteration 2
Based on what we learned from the first iteration, our team first focused on the dynamics of the finger operation. We based the performance off of the DOF tests performed previously. We decided to consolidate the medial and distal portions of the finger for more controllable dynamics. For educational purposes, a MATLAB script was developed from scratch to simulate a 4 bar linkage design. This simulation had adjustable parameters so the performance could be assessed and changed rapidly. Based on this model, several 3D printed mock ups were made to physically assess the performance. A figure from the MATLAB simulation and one iteration of the physical mock up is shown below.
Finger Actuation Raw DOF File
MATLAB Linkage Model and 3D Printed Mock Up
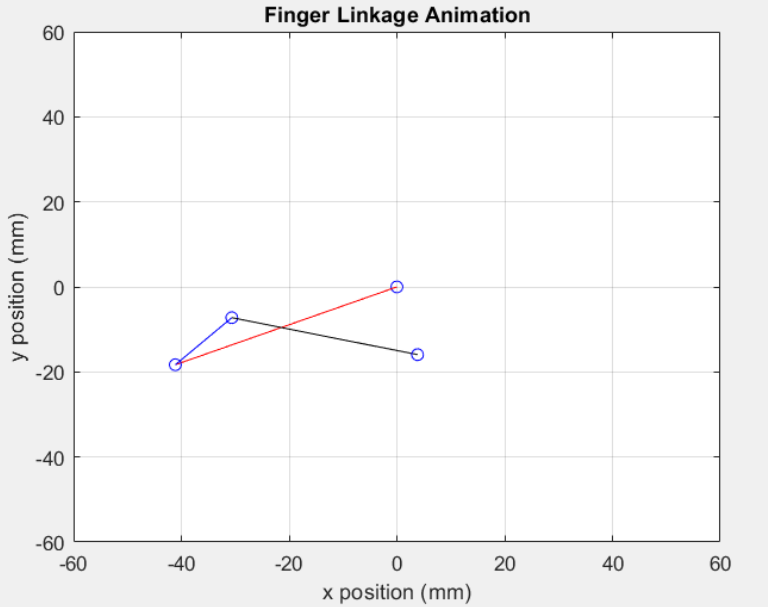
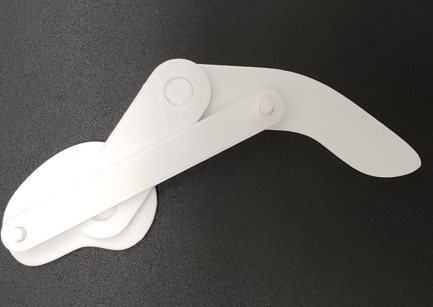
Once the dynamics resembled what was observed in the DOF tests, a 3D mock of the finger was made with an integrated ratcheting system. See below.
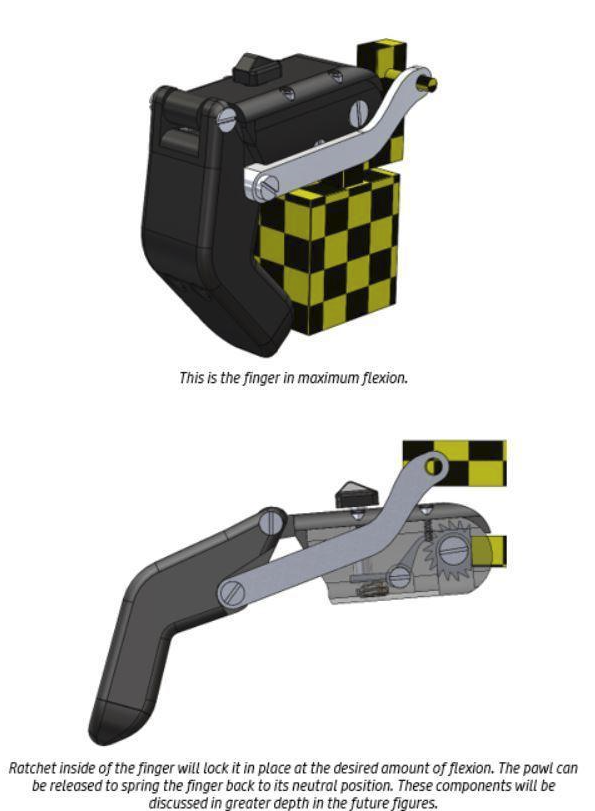
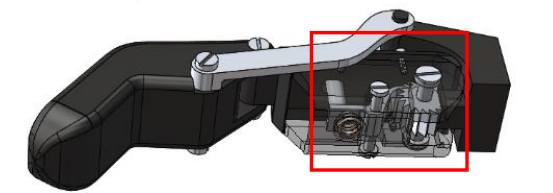
Thumb Prototype
Given the thumb has only a proximal and distal flange, with the users metacarpophalangeal joint unaffected, the need to only design a proximal and distal phalanges also implies that there is a single artificial joint. Because of this, the linkage mobility is 1, and so the prosthetic thumb can be reliably controlled.
Given these design circumstances, the cable driven design was reused and implemented for the thumb. See below.
Thumb Actuation
First Thumb Prototype
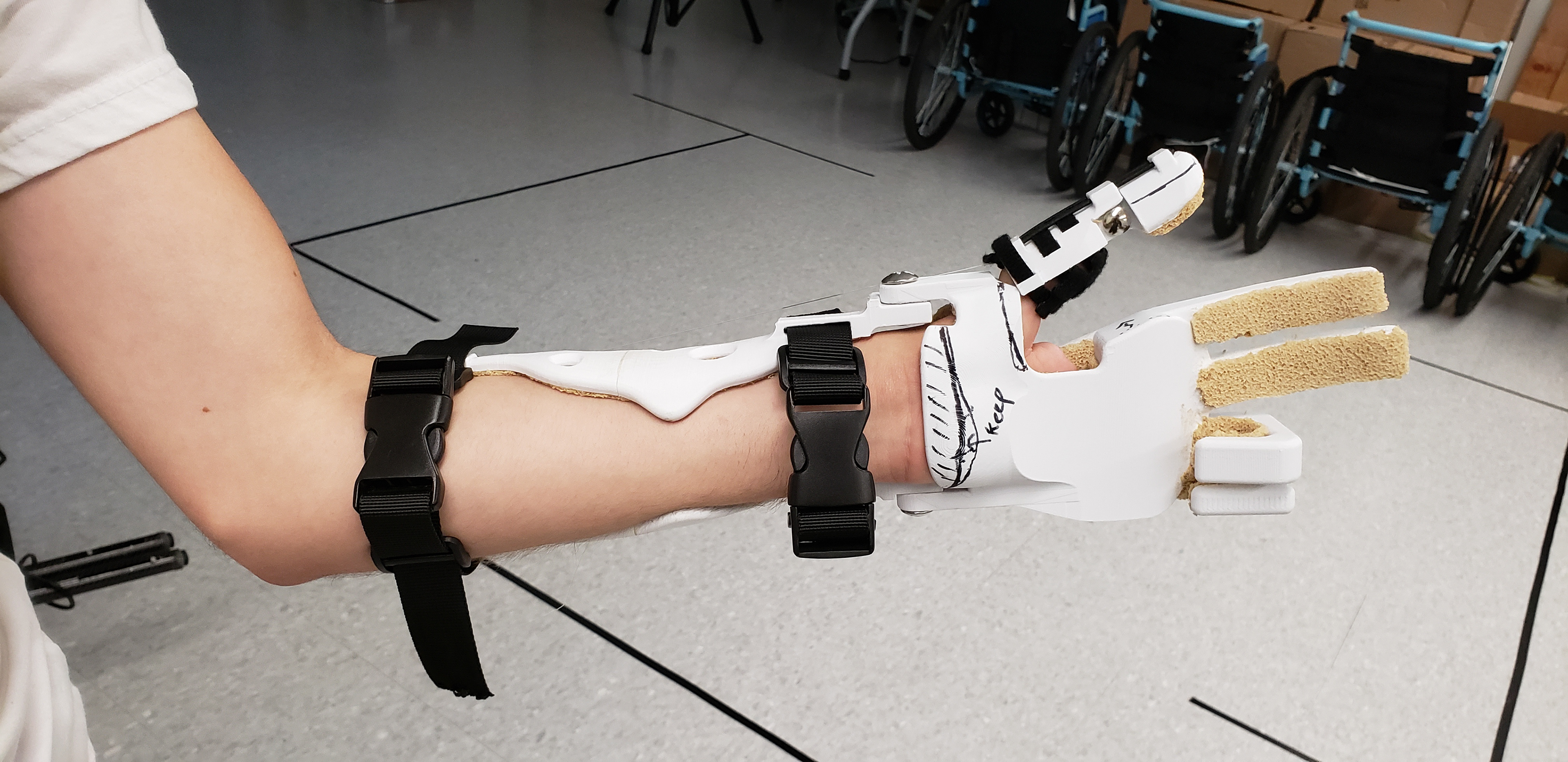
Material Selection
Although resources were limited for this project, the team did investigate various materials for fabrication. A comparison of various materials, including composites, is shown below. For prototyping the form, fit, and function of the prosthetic in the budget and scope of this project, FDM PLA was used.
Tensile Strength versus Density
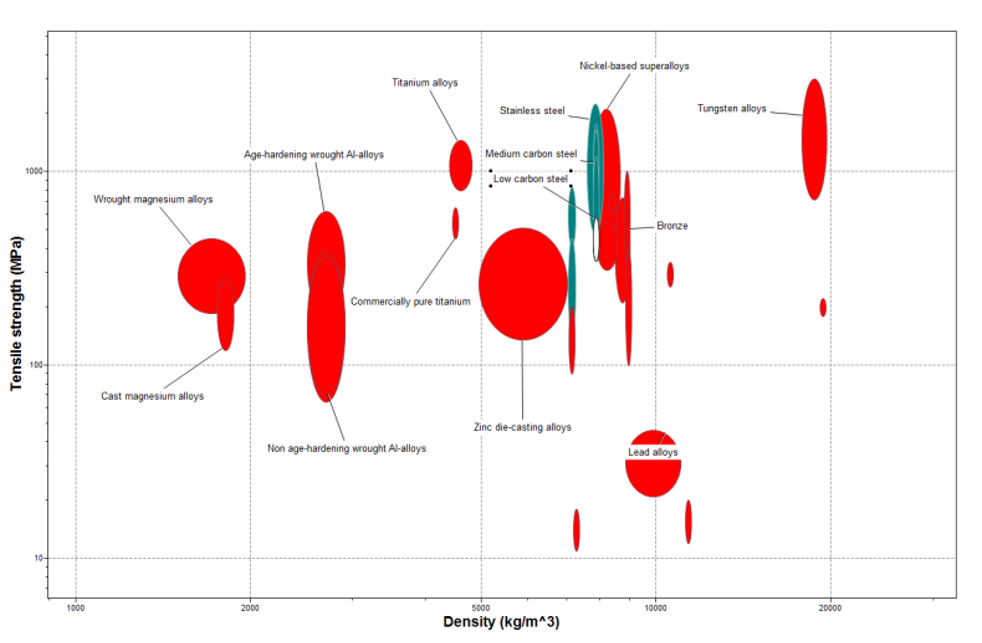
Material Strength Versus Density

Final Prosthetic Images
By consolidating the design solutions as outlined above, and making some minor form changes to do so, we fabricated the complete prosthetic. Potential design solutions and lessons learned will be discussed in a future section titled "Prosthetic Overall Evaluation and Lessons Learned".
Disassembled Prosthetic (Left) and Liquid Rubber Dipping Finger Tips for Grip (Right)
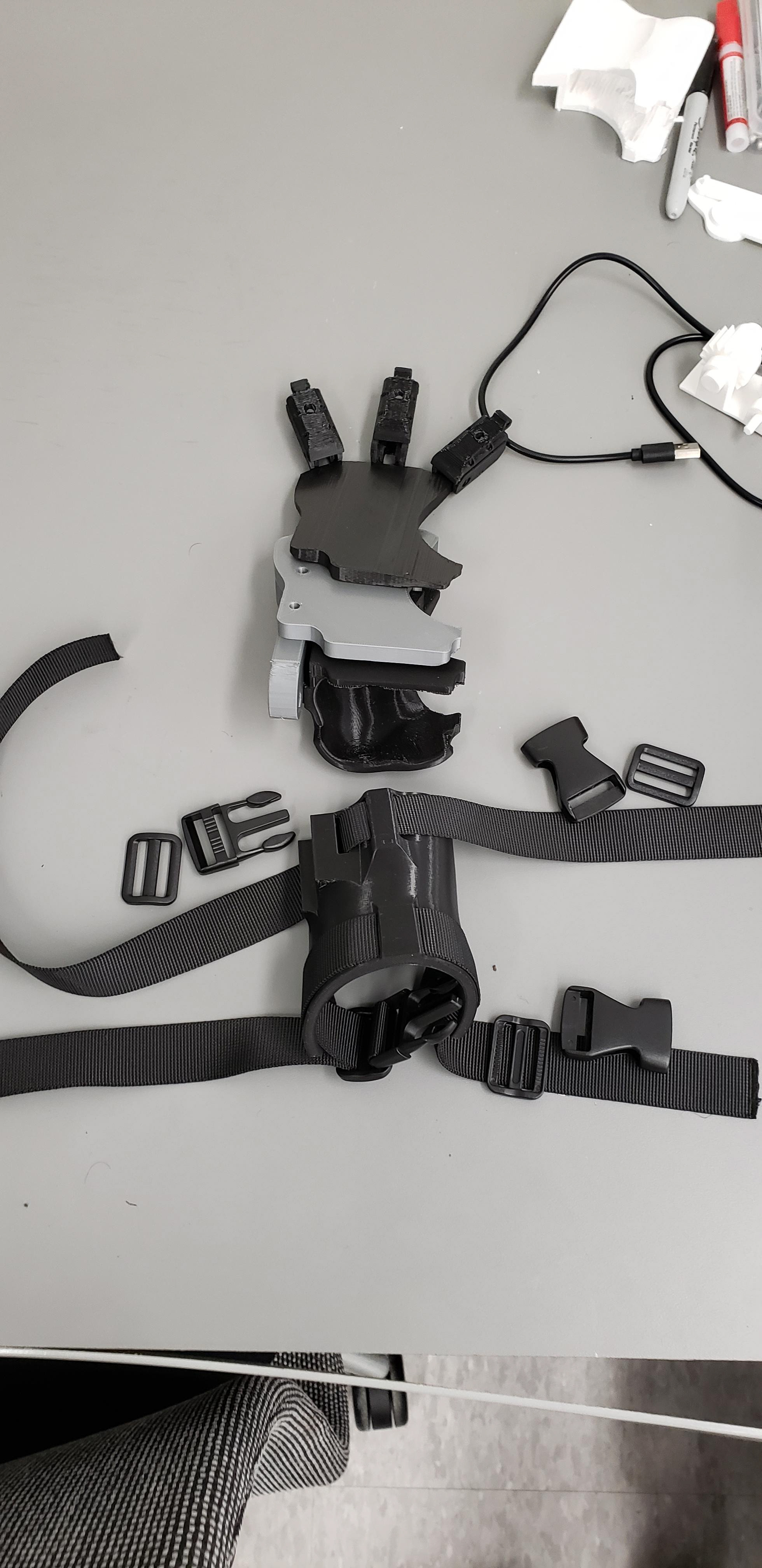
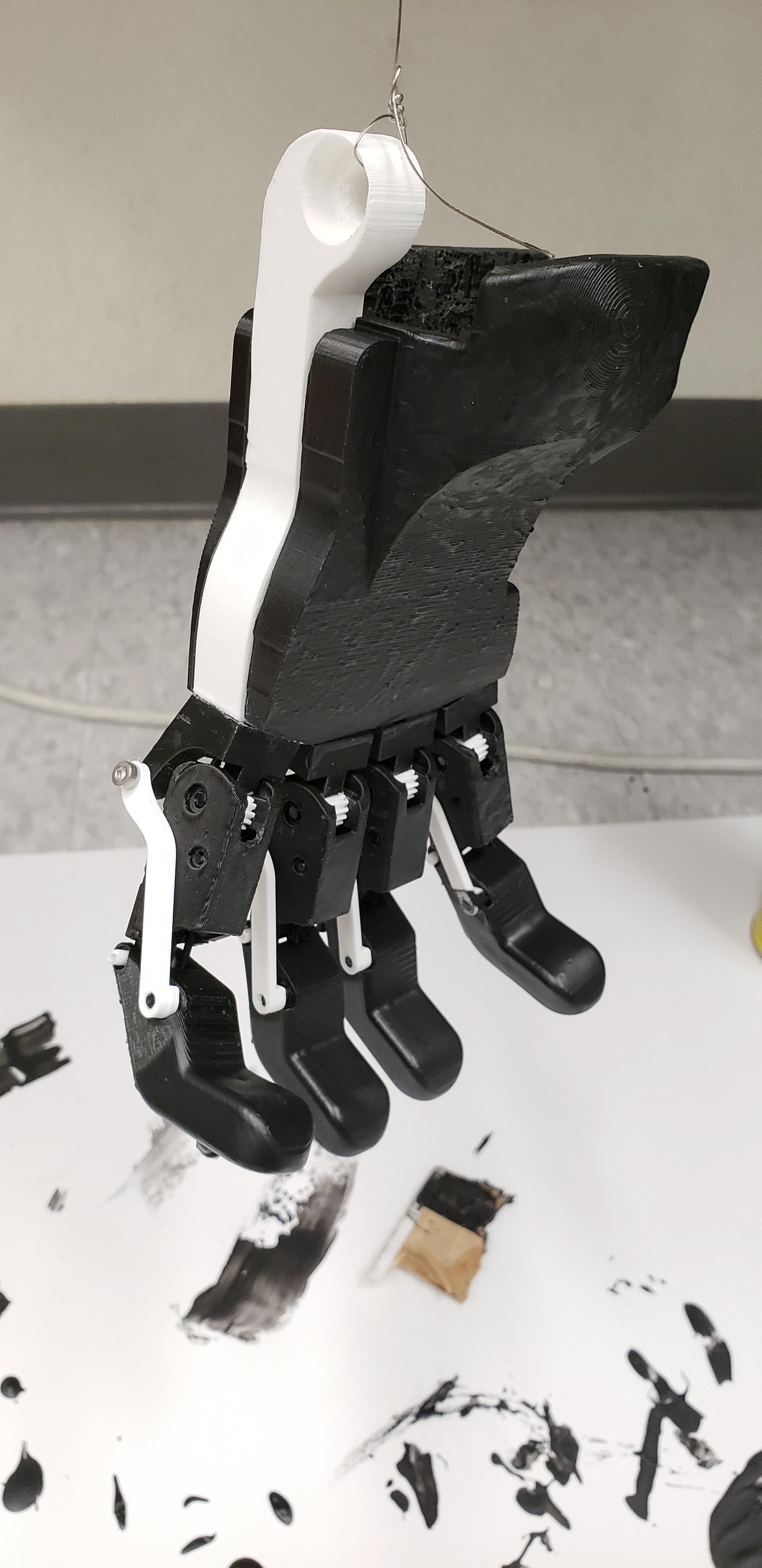
Final Assembled Prosthetic, Excluding Thumb
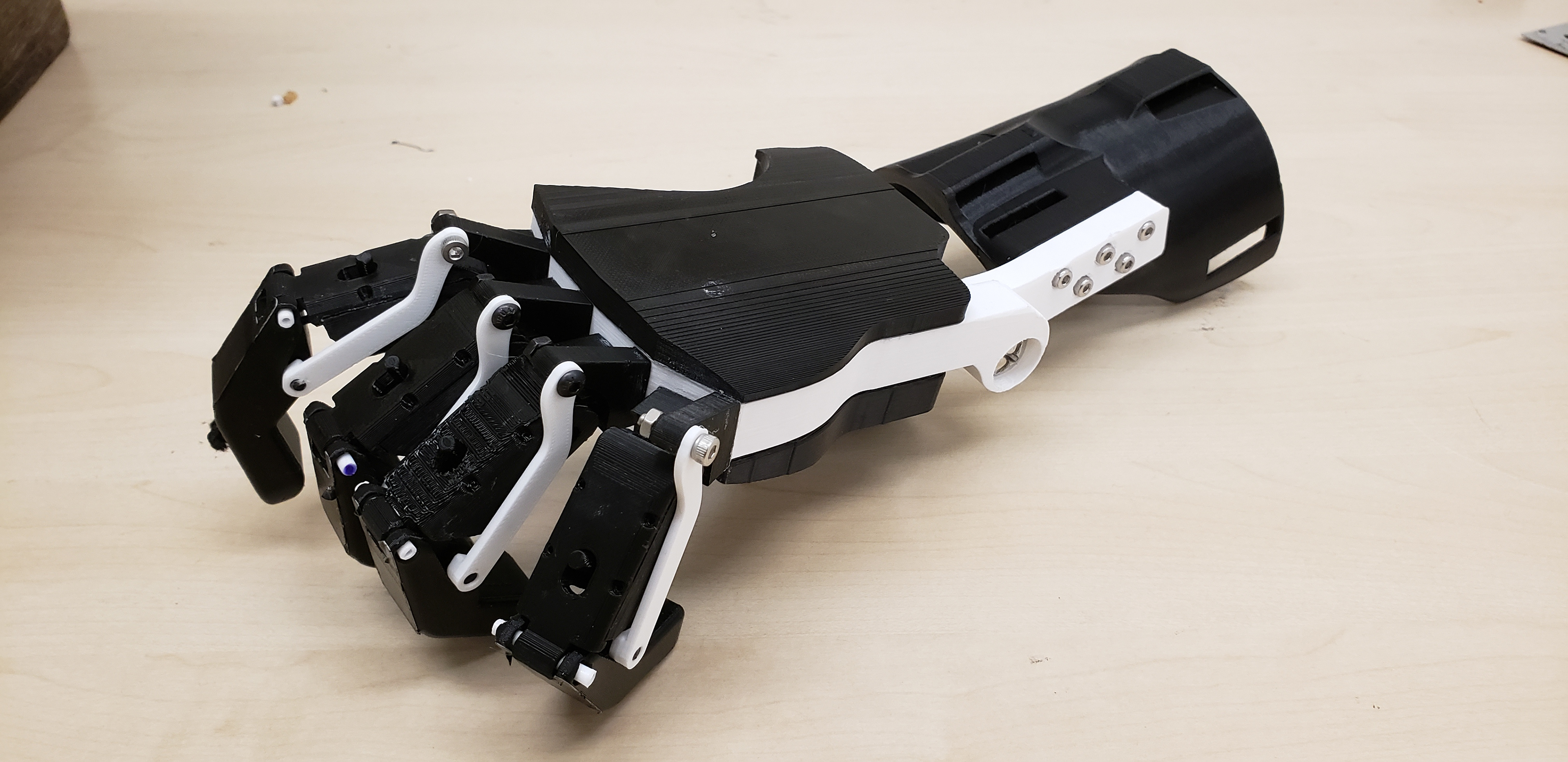
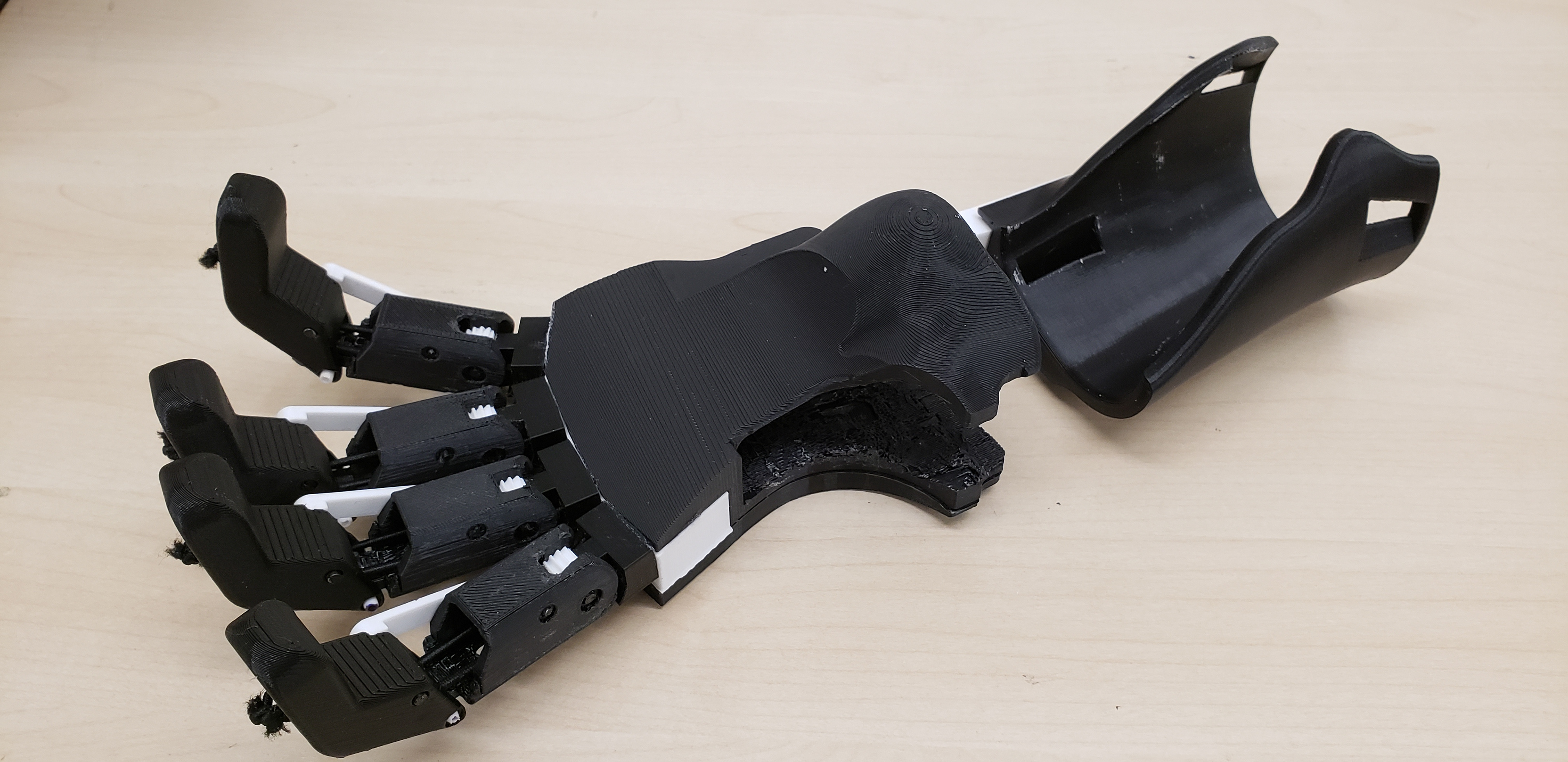
Southampton Hand Assessment Procedure
The Southampton Hand Assessment Procedure (SHAP) is a hand function test used to assess the effectiveness of a prosthetic by analyzing the users ability to pick up various objects with different grasps. Two comparisons are made, one between the prosthetic and the unaffected hand, and one between the prosthetic and the congenitally deficient hand.
There was not much improvement in which the user could achieve certain tasks. However, there was notable improvement in the users ability to pick up certain objects that would have otherwise been impossible to handle. Although this was our last iteration prior to closing the project, the testing could be used for future development. More about future development will be discussed below.
SHAP Test - Example Videos
Other Videos
SHAP Test Results
The result of the SHAP tests gave insight into the functional strengths and areas of improvement for the prosthetic. Some P values are not displayed as they are significantly low enough to be disregarded. That is, the two groups are extremely different, assuming a confidence of 95%. Additionally, for spherical and rectangular prism tests with the deficient hand, the time was maxed out at 12.000s when the user was unable to perform the task (i.e. the user was not able to perform spherical and rectangular prism tests without the assistance of the prosthetic).
1) Compared to the "healthy" unaffected hand, the prosthetic was not able to perform comparably, which is expected.
2) For Power, Tripod, and Tip tests, there was no noticeable improvement in performance.
3) For Spherical and Rectangular Prism tests, the user was able to perform these tests with the prosthetic, and it was impossible to perform these tests without the prosthetic.
4) The prosthetic worsened the users lateral test performance.
With these conclusions, further development could be made to improve the prosthetic by targeting equivalent and worsened performances, learning from these to understand why the performance is equivalent or worsened. From that, the design can be altered to address these fallbacks. Likewise, for the tests that significantly improved the user performance, why was the performance improved? How can these improvements be further developed to perform more closely to the unaffected hand?
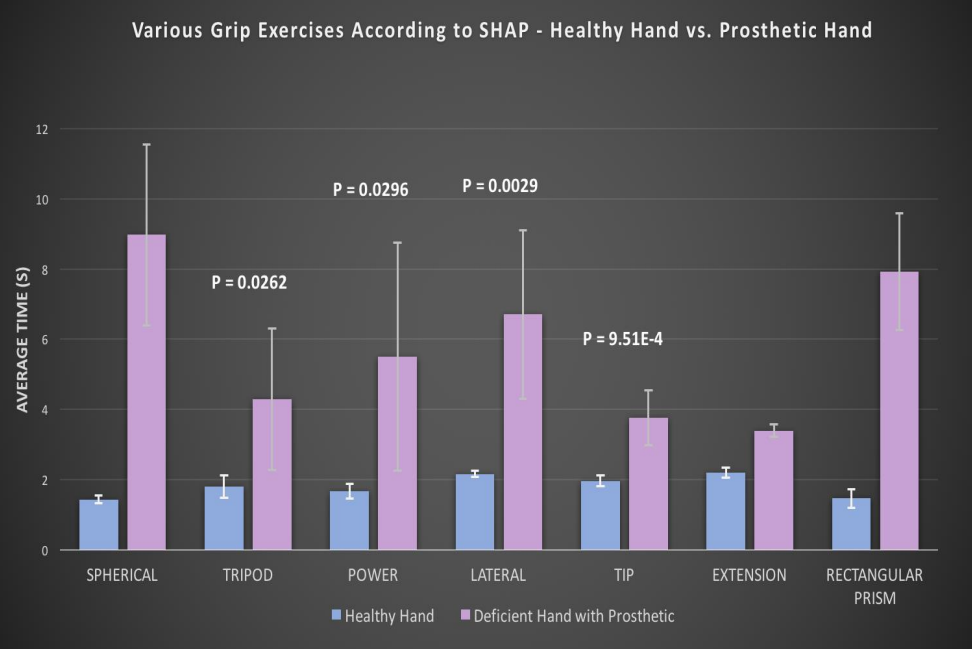
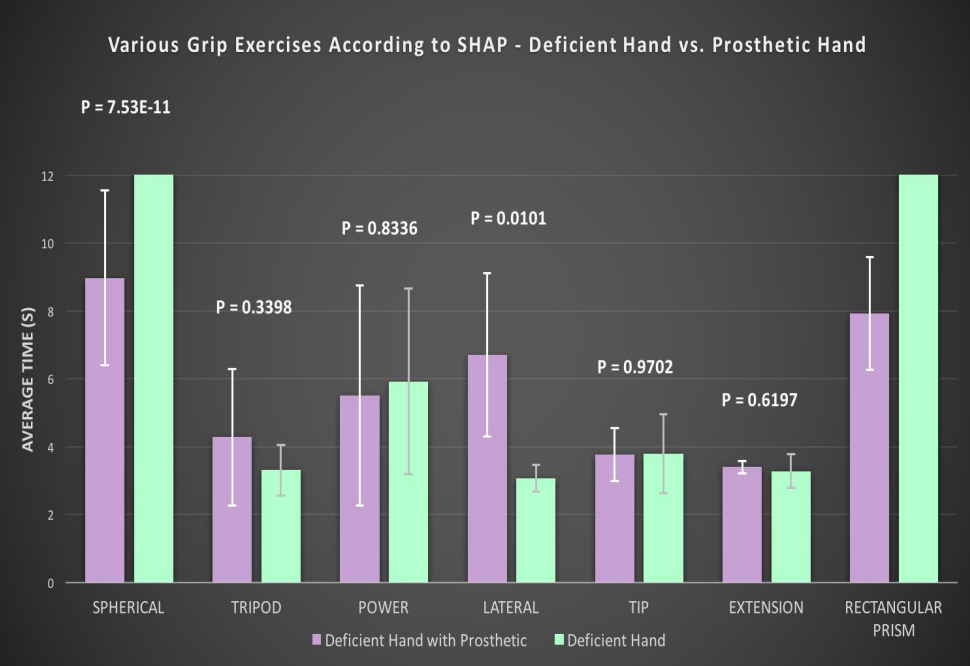
Final Undergraduate Research Opportunities Poster
Citation in poster is listed as (3) and (4)
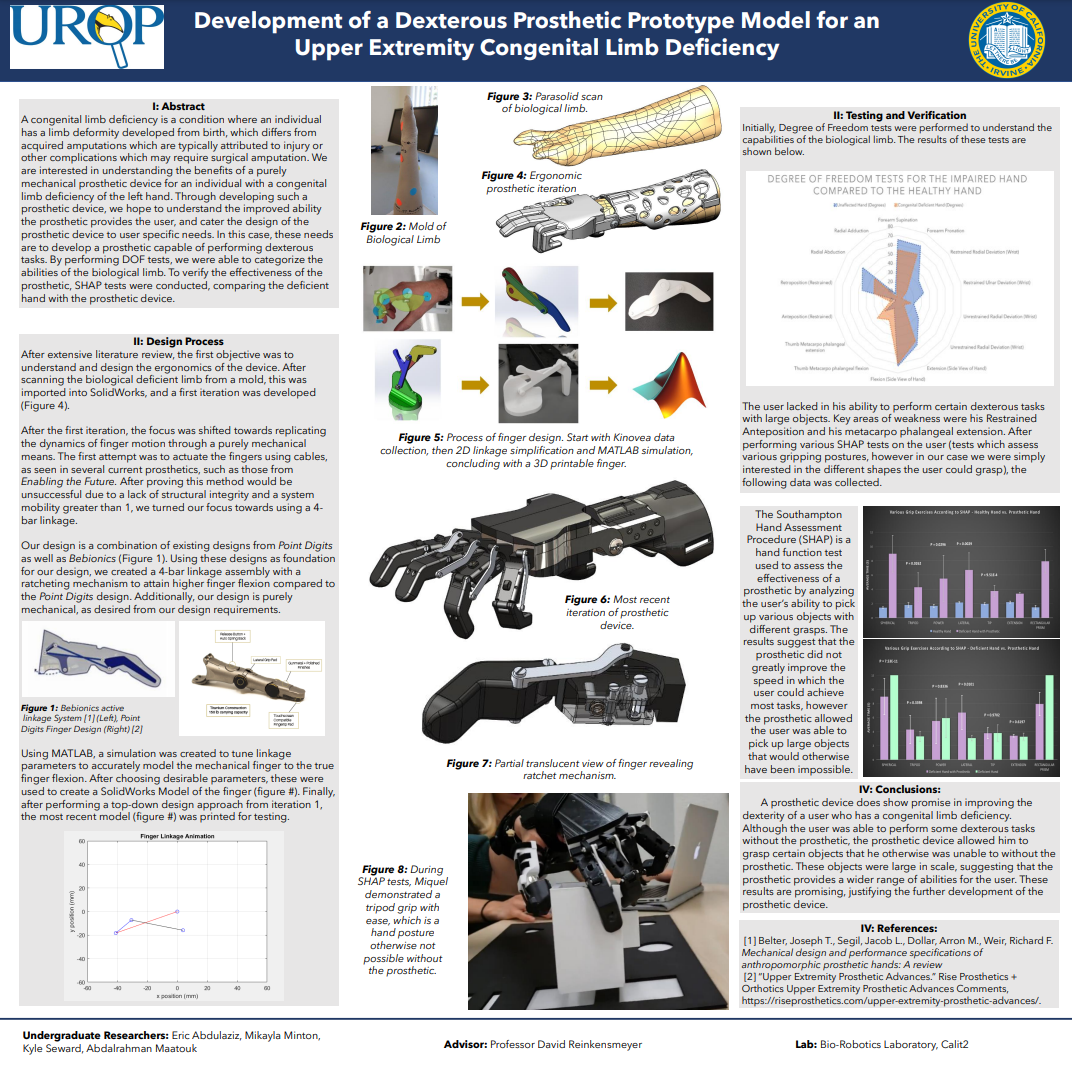
References
(1) Skin Creases - Ifssh.info. https://ifssh.info/TerminologyPdfs/Chapter-5.pdf.
(2) Shin, Young June, et al. “Design of Prosthetic Robot Hand with High Performances Based on Novel Actuation Principles.” IFAC Proceedings Volumes, vol. 46, no. 5, 2013, pp. 313–318., https://doi.org/https://doi.org/10.3182/20130410-3-CN-2034.00111.
(3) Belter Joseph T. Segil, Jacob L., Dollar, Arron M., Weir, Richard F.“
(4) Upper Extremity Prosthetic Advances.” Rise Prosthetics + Orthotics Upper Extremity Prosthetic Advances Comments, https://riseprosthetics.com/upper-extremity-prosthetic-advances/.